현대건설이 국내 최초로 한강을 횡단하는 도로터널 공사에 최첨단 TBM 장비를 도입해 본격 시공에 들어간다. TBM(Tunnel Boring Machine)은 다수의 디스크 커터(cutter)가 장착된 커터 헤드를 회전시켜 암반을 뚫는 원통형 회전식 터널 굴진기로, 발파 공법에 비해 소음, 진동, 분진 등의 발생이 적고 시공성 및 안전성이 높아 전 세계적으로 각광받고 있다.
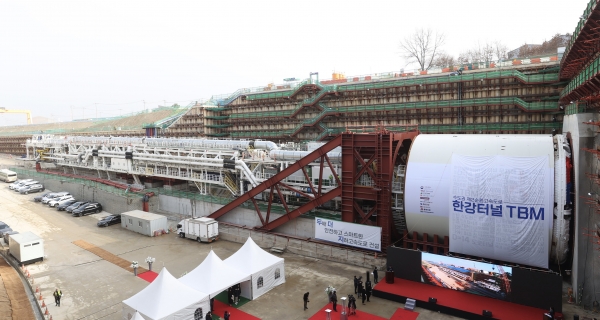
현대건설은 13일 경기도 파주시 소재 ‘고속국도 제400호선 김포~파주간 건설공사 제2공구’ 현장에서 국내 최대 단면 쉴드 TBM 굴진 기념식을 개최했다고 밝혔다. 이날 행사에는 국토교통부 원희룡 장관과 한국도로공사 김일환 사장 직무대행, 국토교통과학기술진흥원 박승기 원장, 현대건설 윤영준 사장 등 정부부처를 비롯한 공공기관 및 시공사 관계자가 참석했다.
‘고속국도 제400호선 김포~파주간 건설공사 제2공구’는 수도권 제2순환고속도로 건설 구간 중 경기 김포시 하성면 마곡리부터 파주시 연다산동을 잇는 총 연장 6.734㎞의 도로로, 한강 밑을 통과하는 2.98㎞ 터널과 나들목, 2개의 교량을 포함한다. 이중에서도 이수식 쉴드 TBM 공법으로 하저를 관통하는 국내 최초의 도로터널 ‘한강터널’이 특히 주목받고 있다.
한강터널 구간은 터널 상부의 흙 두께가 비교적 얕고 수압이 높으며 복합지반으로 이뤄진 고난이도 현장이다. 한강터널 굴진에 사용하는 TBM은 직경 14.01m, 총 길이 125m, 무게 3천184t의 초대형 장비로, 국내 최대 구경(口徑)이자 해외에서도 시공사례가 흔치 않은 규모다. 초대형 프로젝트의 상징성과 더불어 ‘국내 최초 한강 하저를 횡단하는 도로터널 건설’의 의미를 기념하고자 현대건설과 한국도로공사는 지난 7월부터 2개월간 TBM 네이밍 공모전을 실시했다. 뜨거운 관심 속에 1600건이 넘는 아이디어가 접수됐으며, 땅 밑으로 다니기는 동물 중 가장 친숙한 ‘두더지’가 정식 명칭으로 선정됐다.
현대건설은 한강 하저를 가장 안전하게 굴착하기 위해 ‘이수식 쉴드 TBM(Slurry Shield TBM) 공법’을 채택했다. ‘쉴드 TBM’ 공법은 전면부의 커터 헤드가 천천히 회전하며 암반을 깎아내면 굴착된 구간을 두꺼운 콘크리트 구조체로 둘러쌓아 터널 형태를 완성하는 공법이다. 한강터널의 굴착 구간은 굴진과 동시에 사전 제작된 450㎜ 두께의 원형 콘크리트 구조체를 설치해 토사의 붕괴나 유동에 더욱 안전하다. 특히 ‘이수식’은 도심지나 바다, 강 아래 터널을 뚫는 등 상부의 압력이 강하거나 침하를 철저히 방지할 때 적용하는 방식이다. TBM 내 챔버에 이수(물, 점토, 시멘트 등이 섞인 진흙)를 가압·순환시켜 굴진하며, 굴착된 토사는 이수의 흐름을 이용해 지상으로 빼낸다. 대형펌프와 배관설비, 지상의 넓은 부지에 이수처리설비를 구축해야 하는 고가의 공법이지만, 굴진면이 안정되고 강한 수압에 안전하며 공정 효율이 높다.
고난이도 공정인 만큼 현대건설은 경험이 풍부한 독일의 터널 전문가를 영입하고 지반조사를 추가로 실시하는 등 면밀한 준비 과정을 거쳤다. 이번 TBM을 개발한 독일의 헤렌크네히트사(社)와 협업하여 장비에 ▲대기압 커터 교체시스템 ▲디스크 커터 모니터링 시스템 ▲커팅휠 마모감지 센서 ▲전방탐사 시스템 ▲막장 관측 카메라 등 최첨단 기술도 적용했다. 특히 대기압 커터 교체(Accessible Cutter Head) 시스템은 챔버 형태로 제작된 커터 헤드 안에서 유압 개폐장치를 통해 디스크 커터를 교체할 수 있는 장치다. 최근 개발된 기술로 국내 TBM에는 처음 적용됐다. 기존에는 수압이 높은 막장면에 전문 잠수부를 투입해 교체해야 했지만, 해당 시스템을 도입하면 작업자가 대기압 상태에서 작업할 수 있다.
TBM 커터 헤드에는 71개의 디스크 커터가 장착돼있다. 단단한 암반을 뚫는 핵심 부품이기에 마모 상태를 수시로 확인해 교체해야 한다. 전체 굴착에 사용될 디스크 커터는 총 2천5백여 개로, 대기압 커터 교체 시스템을 통해 안전 확보는 물론 획기적인 공정 효율 개선이 예상된다.
이외에도 디스크 커터의 회전수와 온도 정보를 실시간 모니터링해 교체시기 및 비정상 마모 등을 확인할 수 있는 디스크 커터 모니터링(Disc Cutter Rotation Monitoring) 시스템, 센서를 통해 면판의 마모 정도를 측정하는 마모 감지 센서 시스템(Wear Detection System), 지진파(충격파)의 속도차이를 이용해 TBM 전방 지질 변화를 예측할 수 있는 전방탐사 시스템(Advance Exploration System), 외부 막장면과 커터 헤드 챔버 내부 및 후면을 육안 관찰할 수 있는 막장 관측 카메라(Telescopic Camera) 등 최첨단 기술을 갖춰 시공성과 안전성을 더욱 강화했다.
한편 현대건설은 안전하고 효과적인 현장 운영을 위해 다양한 스마트 기술을 적용한다. 자체 개발한 TADAS를 통해 각종 굴착 데이터와 지반 정보 등을 실시간으로 취합·분석하고, BIM 기반의 디지털 관리 시스템 HIBoard, 중앙 통합 운영 시스템 HOC 등을 도입해 현장을 원격 지원·관리한다. 더불어 ICT 기반의 무선 통신 환경을 구축해 터널 전 구간의 원활한 데이터 통신은 물론 다양한 스마트 건설장비를 활용할 수 있는 토대도 마련한다.
공정 전 과정의 안전관리는 IoT 센서 기반의 안전관리시스템, AI 재해예측시스템 등 현대건설의 독자적인 기술 노하우가 집약된 시스템을 통해 철저하게 이뤄진다. 원격드론, 무인지상차량 등을 활용해 무인 현장 관리를 실현하며 이동식 CCTV, AI 영상인식 장비협착방지시스템 등을 설치해 안전관리 사각지대를 최소화할 계획이다.
현대건설은 싱가포르 남북 전력구 터널 NS3 공사, 대곡~소사 복선전철 등 국내외 26개 현장의 TBM 터널을 건설하며 전문적인 시공 경험을 축적해왔다. 세계 최초로 개발한 시험 장비와 다수의 특허를 보유한 것은 물론 TBM 관련 분야 연구에서 지속적인 성과를 내며 세계적 수준의 기술력을 인정받고 있다.
뿐만 아니라 현대건설은 국내 최초 ‘한국형 로드헤더 기계 굴착속도 예측모델’을 개발하고 관련 특허를 등록하는 등 터널 기계화 시공에 앞장서고 있다. 다양한 연구개발 결과는 인천도시철도 1호선 검단연장선 현장 등에 실제 적용해 공기 단축·공사비 절감 등의 성과를 입증한 바 있다.
댓글
(0) 로그아웃